Barcode labels have become an indispensable tool in managing and organizing inventory, assets, and various processes within a facility. Implementing barcode labels can streamline operations, enhance efficiency, and reduce errors. If you’re considering integrating barcode labels into your facility, here’s a step-by-step guide to help you get started and examples of how they can be used in your facility.
Define Your Objectives:
Before diving into the world of barcode labels, clearly define your goals and objectives. Determine what aspects of your facility’s operations you want to improve – whether it’s inventory management, asset tracking, or enhancing overall efficiency.
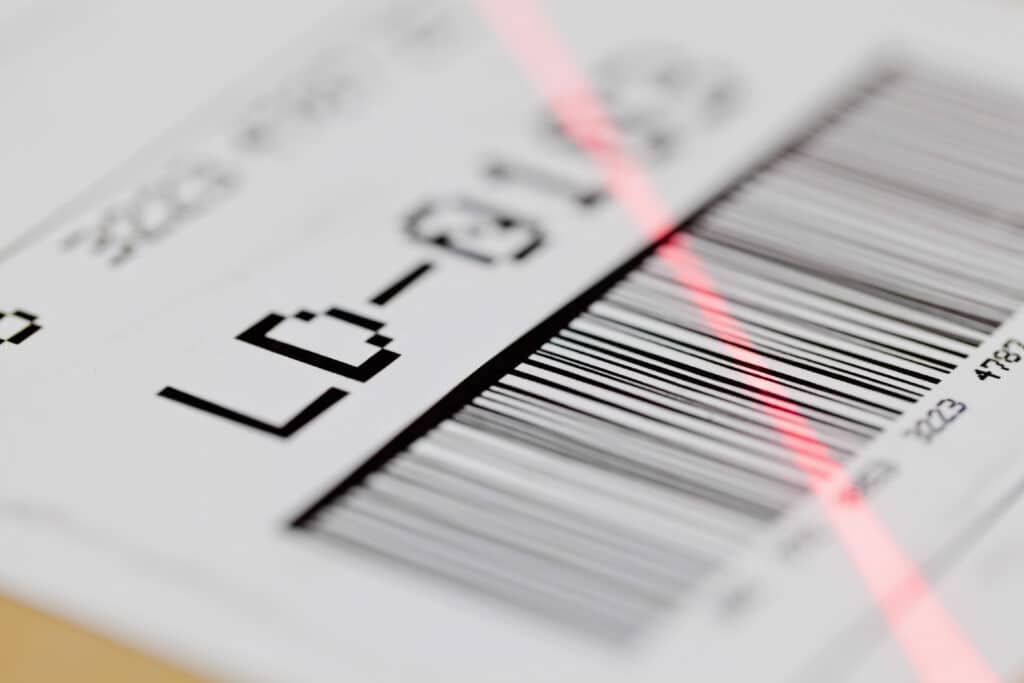
Select the Right Barcode System:
There are various types of barcodes, each serving different purposes. Common types include UPC, QR codes, and Code 39. Choose a barcode system that aligns with your specific needs. Consider factors such as data capacity, readability, and compatibility with your existing systems.
Invest in Barcode Scanners:
To effectively utilize barcode labels, you’ll need reliable barcode scanners. Choose scanners that are compatible with the barcode type you’ve selected. Some facilities opt for handheld scanners, while others prefer fixed or mounted scanners depending on the nature of their operations.
Choose Suitable Labeling Material:
Barcode labels come in different materials, including paper, polyester, and vinyl. Consider the environmental conditions within your facility – factors like temperature, moisture, and exposure to chemicals. Select labeling materials that can withstand these conditions to ensure longevity and readability.
Design and Print Your Barcode Labels:
Create a standardized design for your barcode labels to ensure consistency and ease of identification. Utilize barcode label design software to generate unique barcodes for each item or asset. Invest in a high-quality barcode label printer to ensure the image is scannable.
Implement a Barcode Database:
Establish a centralized database to manage and store information associated with each barcode. This database should include details like item descriptions, serial numbers, and locations. This step is crucial for efficient tracking and management of assets or inventory.
Train Your Team:
Educate your staff on the importance of barcode labels and provide training on how to use barcode scanners effectively. This step is vital for a smooth transition and the successful implementation of the barcode system.
Test and Iterate:
Before fully integrating barcode labels into your operations, conduct thorough testing to identify any potential issues. This step allows you to make necessary adjustments and refine your barcode system for optimal performance.
Scale Up Gradually:
Implement barcode labels in stages to minimize disruptions. Start with a specific area or department, gather feedback, and make improvements before expanding the use of barcode labels throughout the entire facility.
Monitor and Maintain:
Regularly monitor the performance of your barcode system and conduct routine maintenance to address any issues promptly. Stay informed about advancements in barcode technology to ensure your facility benefits from the latest innovations.
Integrating barcode labels into your facility can significantly enhance operational efficiency and accuracy. By following these steps, you can seamlessly implement a barcode system that meets your facility’s unique needs and sets the foundation for improved management and productivity. Still not sure where to start? Here are some examples of ways you can use barcode labels in your facility.
Inventory Management:
Barcode labels are invaluable for tracking inventory levels accurately. Assign unique barcodes, or UPCs (universal product codes), to each product, making it easy to scan items in and out. This streamlines the replenishment process, minimizes errors, and ensures that you always have real-time visibility into your stock levels.
Asset Tracking:
Efficiently manage and monitor your facility’s assets by affixing barcode labels to equipment, tools, and machinery. This facilitates quick and accurate identification, allowing for easy tracking of asset movements, maintenance schedules, and depreciation.
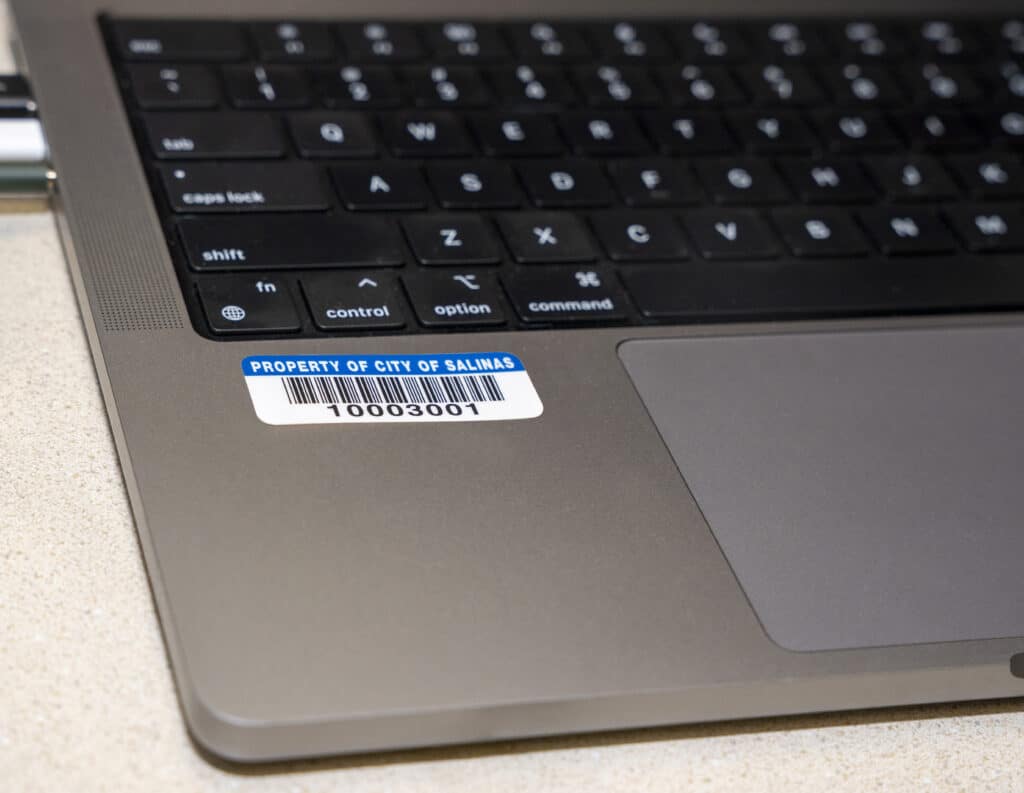
Order Fulfillment:
Improve order accuracy and reduce processing times by using barcode labels in the order fulfillment process. Attach labels to products and packages, enabling warehouse staff to scan items quickly and verify orders with precision, reducing the likelihood of errors.
Quality Control:
Enhance quality control procedures by implementing barcode labels. Attach labels to products during different stages of production, allowing for easy tracking and identification of batches. This ensures that quality checks are performed consistently and documented accurately.
Work-in-Progress (WIP) Tracking:
Monitor the progress of ongoing projects or manufacturing processes by utilizing barcode labels on work-in-progress items. This enables real-time tracking of production stages, helping to identify bottlenecks and improve overall workflow efficiency.
Time and Attendance Tracking:
Simplify time and attendance tracking for employees by incorporating barcode labels into your employee identification system. Employees can use barcode badges to clock in and out, providing an automated and accurate record of working hours.
Maintenance Management:
Streamline maintenance operations by tagging equipment and machinery with barcode labels. Maintenance personnel can quickly access equipment history, schedule preventive maintenance, and record repairs, ensuring optimal functionality and reducing downtime.
Document Management:
Improve document organization and retrieval by applying barcode labels to files, folders, and documents. This is especially beneficial in large facilities where efficient document tracking and access are essential for regulatory compliance and operational efficiency.
Shipping and Receiving:
Expedite the shipping and receiving process by using barcode labels on packages and shipments. This facilitates quick and accurate scanning at each stage of the logistics chain, reducing errors and enhancing the overall efficiency of your supply chain.
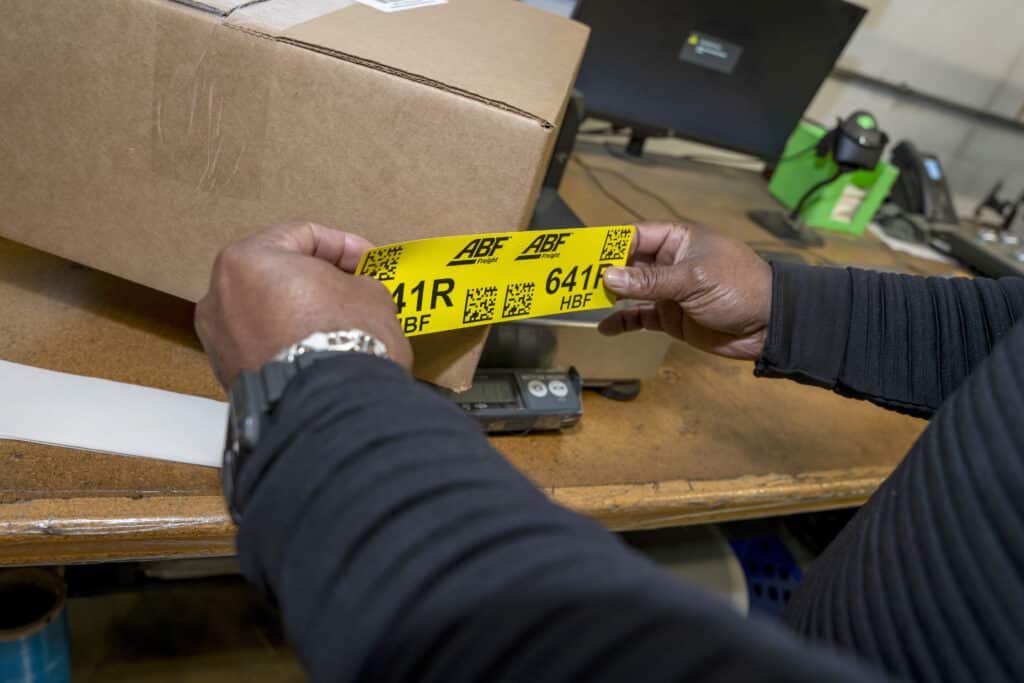
Batch and Lot Tracking:
Ensure traceability for products with specific batch or lot numbers by incorporating barcode labels. This is crucial in industries such as pharmaceuticals and food production, where tracking the origin and movement of each batch is a regulatory requirement.
By incorporating barcode labels into these various aspects of your facility’s operations, you can unlock new levels of efficiency, accuracy, and traceability, ultimately contributing to the overall success of your organization. Contact Chicago Tag & Label to get started!